A composição química da areia cerâmica é principalmente Al2O3 e SiO2, e a fase mineral da areia cerâmica é principalmente fase corindo e fase mulita, bem como uma pequena quantidade de fase amorfa.A refratariedade da areia cerâmica é geralmente superior a 1800°C, e é um material refratário de alumínio-silício de alta dureza.
Características da areia cerâmica
● Alta refratariedade;
● Baixo coeficiente de dilatação térmica;
● Alta condutividade térmica;
● Forma esférica aproximada, fator de ângulo pequeno, boa fluidez e capacidade de compactação;
● Superfície lisa, sem rachaduras, sem saliências;
● Material neutro, adequado para vários materiais metálicos fundidos;
● As partículas possuem alta resistência e não se quebram com facilidade;
● A faixa de tamanho de partícula é ampla e a mistura pode ser personalizada de acordo com os requisitos do processo.
Aplicação de Areia Cerâmica em Fundições de Motores
1. Use areia de cerâmica para resolver a deformação de veios, aderência de areia, núcleo quebrado e núcleo de areia da cabeça do cilindro de ferro fundido
● Bloco de cilindro e cabeçote são as peças fundidas mais importantes do motor
● A forma da cavidade interna é complexa e os requisitos de precisão dimensional e limpeza da cavidade interna são altos
● Grande lote

A fim de garantir a eficiência da produção e a qualidade do produto,
● A produção de linha de montagem de areia verde (principalmente linha de modelagem hidrostática) é geralmente usada.
● Os núcleos de areia geralmente usam o processo de caixa fria e areia revestida com resina (núcleo shell), e alguns núcleos de areia usam o processo de caixa quente.
● Devido à forma complexa do núcleo de areia do bloco de cilindros e da carcaça do cabeçote, alguns núcleos de areia têm uma pequena área de seção transversal, a parte mais fina de alguns blocos de cilindros e núcleos de camisa de água do cabeçote é de apenas 3-3,5 mm e a saída de areia é estreita, o núcleo de areia após a fundição é cercado por ferro fundido em alta temperatura por um longo tempo, é difícil limpar a areia e é necessário equipamento de limpeza especial, etc. No passado, toda a areia de sílica era usada na fundição produção, o que causou problemas de veios e aderência de areia nas peças fundidas da camisa d'água do bloco e do cabeçote do cilindro.Deformação do núcleo e problemas de núcleo quebrado são muito comuns e difíceis de resolver.
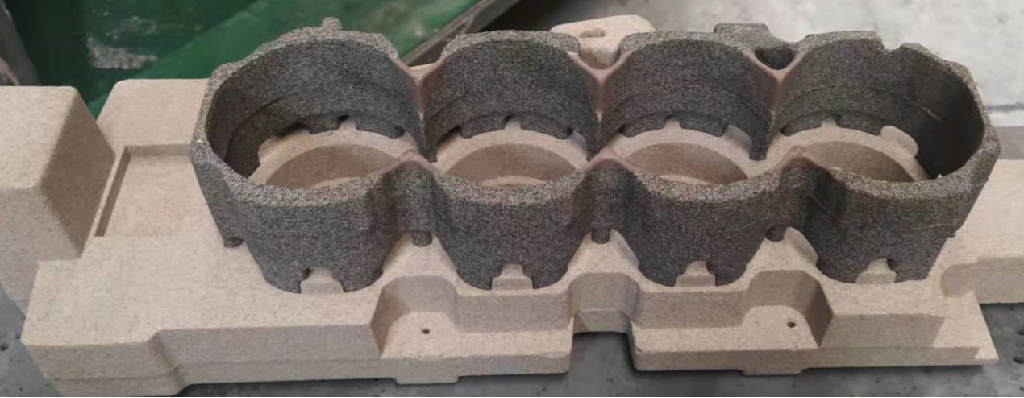
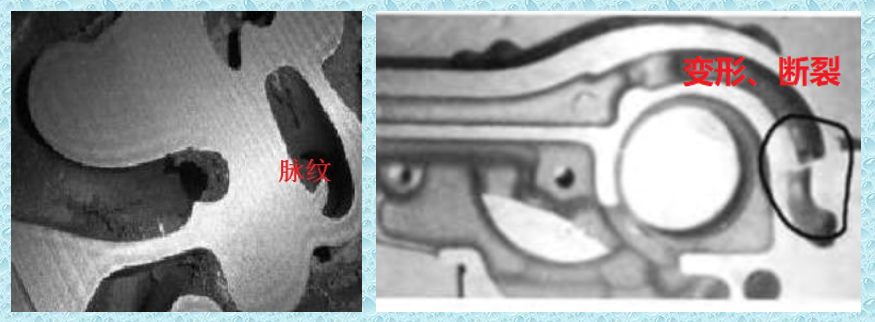
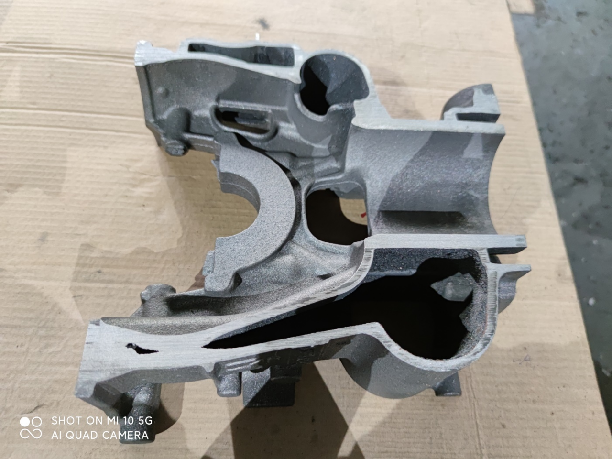
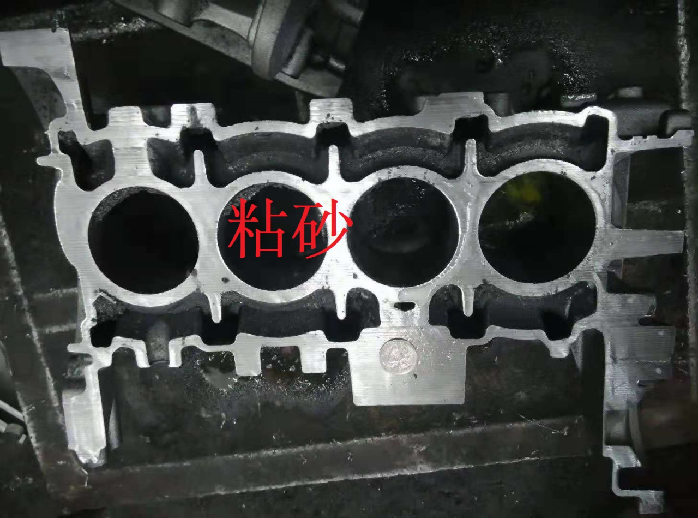
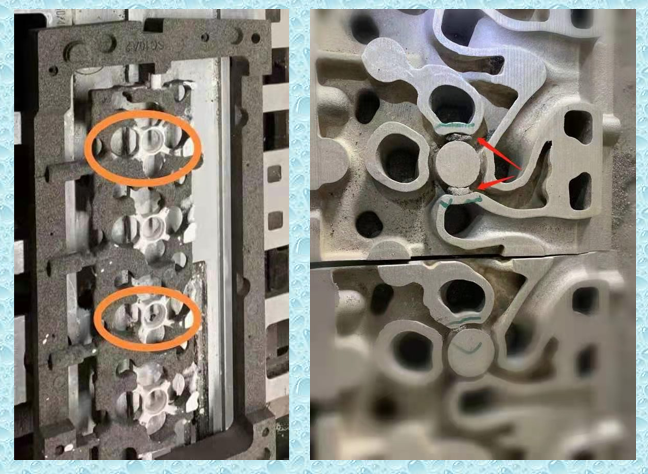
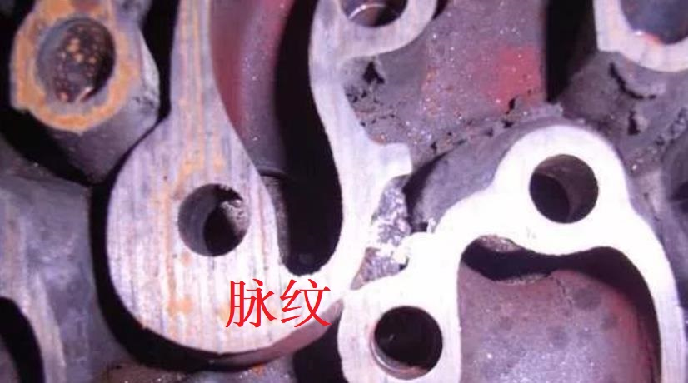
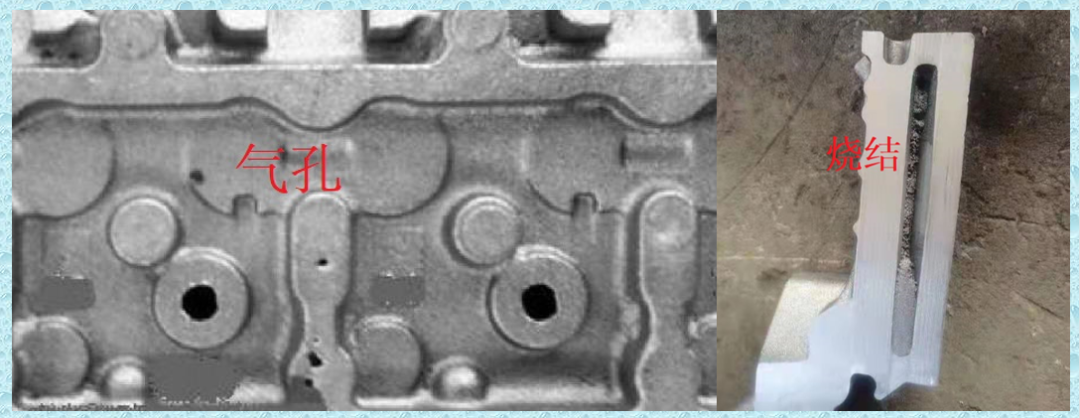
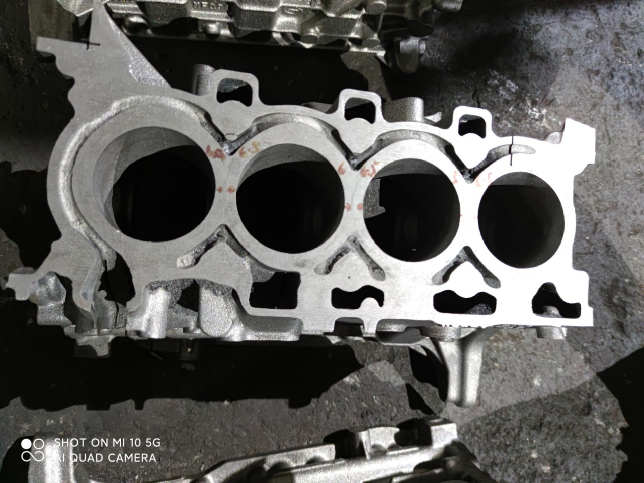
Para resolver tais problemas, a partir de 2010, algumas empresas nacionais de fundição de motores bem conhecidas, como FAW, Weichai, Shangchai, Shanxi Xinke, etc., começaram a pesquisar e testar a aplicação de areia cerâmica para produzir blocos de cilindros, camisas de água do cabeçote e passagens de óleo.Núcleos de areia iguais efetivamente eliminam ou reduzem defeitos como sinterização da cavidade interna, aderência de areia, deformação do núcleo de areia e núcleos quebrados.
As fotos a seguir são feitas por areia de cerâmica com processo de caixa fria.
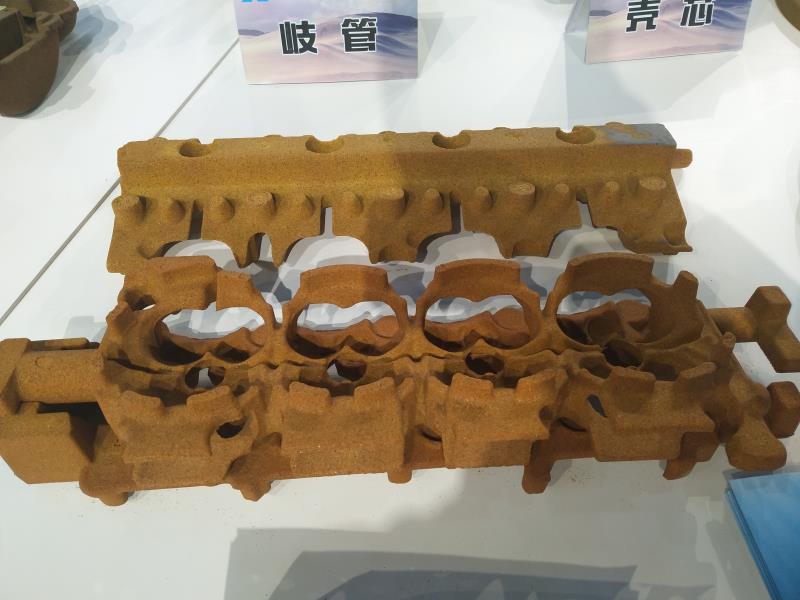
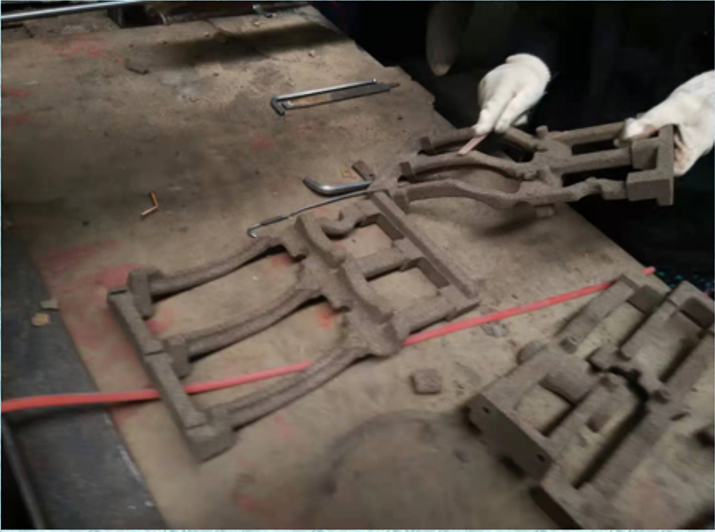
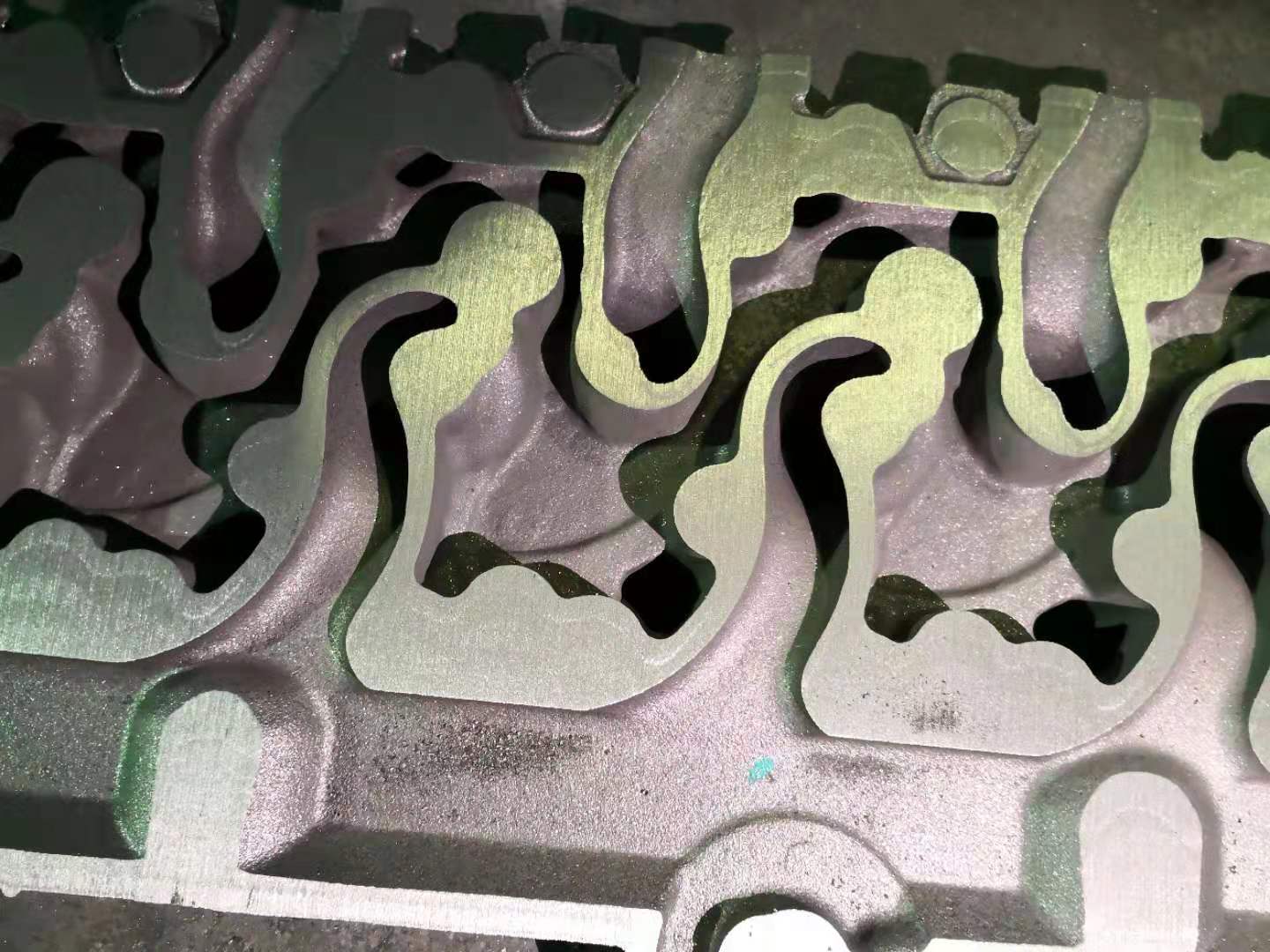
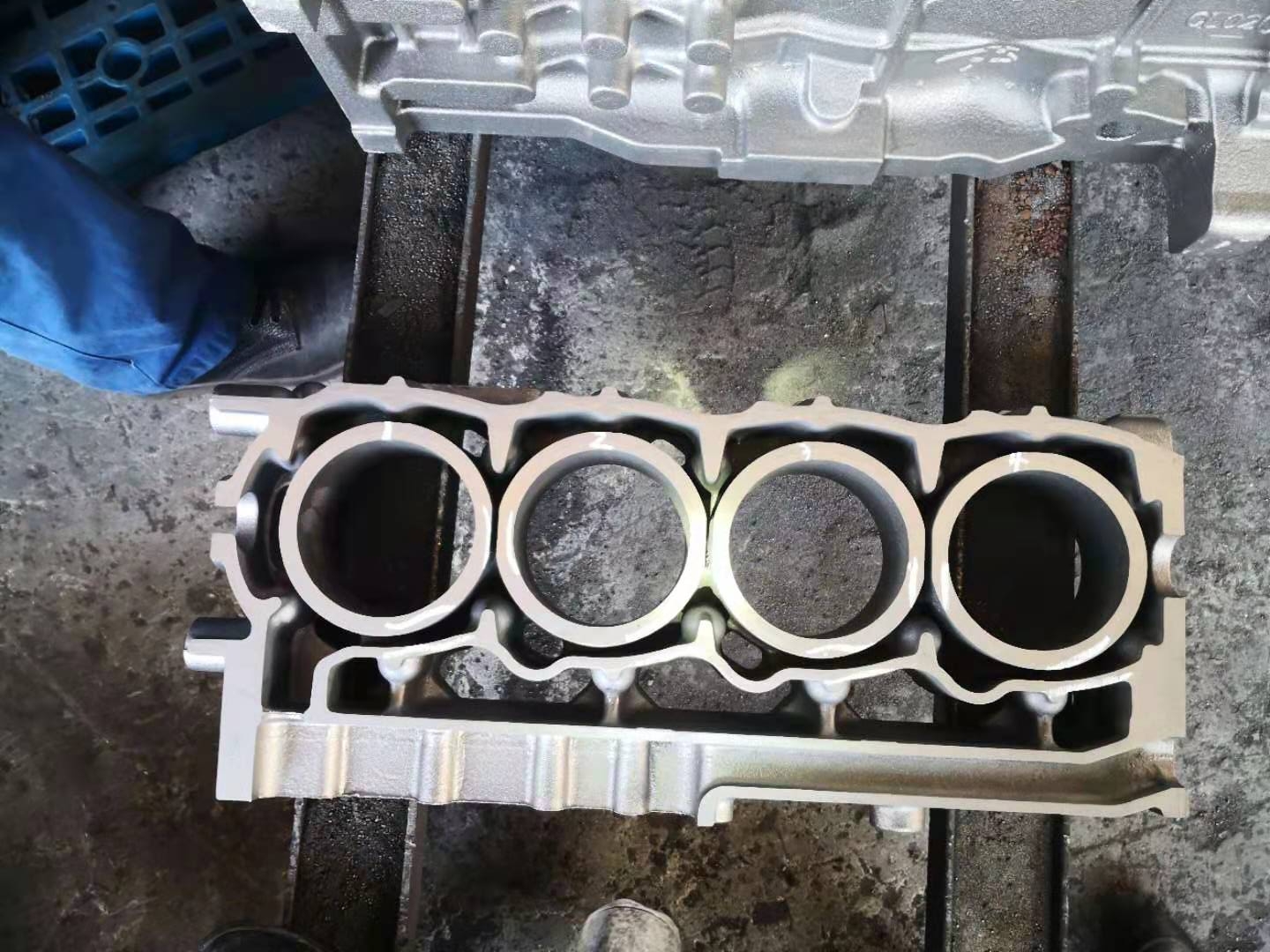
Desde então, a areia de depuração misturada com areia cerâmica foi gradualmente promovida em processos de caixa fria e caixa quente e aplicada aos núcleos da camisa de água do cabeçote do cilindro.Está em produção estável há mais de 6 anos.O uso atual do núcleo de areia de caixa fria é: de acordo com a forma e tamanho do núcleo de areia, a quantidade de areia de cerâmica adicionada é de 30% a 50%, a quantidade total de resina adicionada é de 1,2% a 1,8% e a a resistência à tração é de 2,2-2,7 MPa.(Dados de teste de amostra de laboratório)
Resumo
Bloco de cilindro e peças de ferro fundido da cabeça contêm muitas estruturas de cavidade interna estreitas, e a temperatura de vazamento é geralmente entre 1440-1500°C.A parte de paredes finas do núcleo de areia é facilmente sinterizada sob a ação de ferro fundido de alta temperatura, como infiltração de ferro fundido no núcleo de areia, ou produz reação de interface para formar areia pegajosa.A refratariedade da areia de cerâmica é maior que 1800°C, entretanto, a verdadeira densidade da areia de cerâmica é relativamente alta, a energia cinética das partículas de areia com o mesmo diâmetro e velocidade é 1,28 vezes maior que a das partículas de areia de sílica ao atirar areia, que pode aumentar a densidade dos núcleos de areia.
Essas vantagens são as razões pelas quais o uso de areia cerâmica pode resolver o problema de aderência de areia na cavidade interna das peças fundidas do cabeçote.
A camisa de água, as peças de admissão e escape do bloco de cilindros e do cabeçote geralmente apresentam defeitos de veios.Um grande número de pesquisas e práticas de fundição mostraram que a causa raiz dos defeitos de veias na superfície da fundição é a expansão da mudança de fase da areia de sílica, que causa estresse térmico, leva a rachaduras na superfície do núcleo de areia, o que causa ferro fundido para penetrar nas fissuras, a tendência dos veios é maior principalmente no processo cold box.De fato, a taxa de expansão térmica da areia de sílica é tão alta quanto 1,5%, enquanto a taxa de expansão térmica da areia de cerâmica é de apenas 0,13% (aquecida a 1000°C por 10 minutos).A possibilidade de rachaduras é muito pequena na superfície do núcleo de areia devido ao estresse de expansão térmica.O uso de areia cerâmica no núcleo de areia do bloco e cabeçote é atualmente uma solução simples e eficaz para o problema de veios.
Núcleos de areia de revestimento de água de cabeça de cilindro complicados, de paredes finas, longos e estreitos e núcleos de areia de canal de óleo de cilindro exigem alta resistência (incluindo resistência a alta temperatura) e tenacidade e, ao mesmo tempo, precisam controlar a geração de gás da areia do núcleo.Tradicionalmente, o processo de areia revestida é o mais utilizado.O uso de areia cerâmica reduz a quantidade de resina e consegue o efeito de alta resistência e baixa geração de gás.Devido à melhoria contínua do desempenho da resina e da areia bruta, o processo de caixa fria tem substituído cada vez mais parte do processo de areia revestida nos últimos anos, melhorando consideravelmente a eficiência da produção e melhorando o ambiente de produção.
2. Aplicação de areia de cerâmica para resolver o problema de deformação do núcleo de areia do tubo de escape
Os coletores de escape funcionam sob condições alternadas de alta temperatura por um longo tempo, e a resistência à oxidação dos materiais em altas temperaturas afeta diretamente a vida útil dos coletores de escape.Nos últimos anos, o país melhorou continuamente os padrões de emissão do escapamento automotivo, e a aplicação da tecnologia catalítica e da tecnologia de turboalimentação aumentou significativamente a temperatura de trabalho do coletor de escapamento, atingindo acima de 750 °C.Com a melhoria adicional do desempenho do motor, a temperatura de trabalho do coletor de escape também aumentará.Atualmente, aço fundido resistente ao calor é geralmente usado, como ZG 40Cr22Ni10Si2 (JB/T 13044), etc., com uma temperatura resistente ao calor de 950°C-1100°C.
A cavidade interna do coletor de escape geralmente deve estar livre de rachaduras, fechamentos a frio, cavidades de contração, inclusões de escória, etc. que afetam o desempenho, e a rugosidade da cavidade interna não deve ser maior que Ra25.Ao mesmo tempo, existem regulamentos rígidos e claros sobre o desvio da espessura da parede do tubo.Por muito tempo, o problema da espessura irregular da parede e do desvio excessivo da parede do tubo do coletor de escape tem atormentado muitas fundições de coletores de escape.

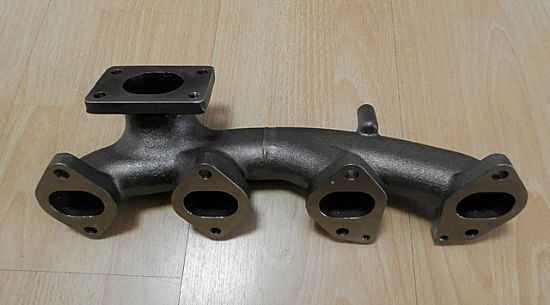
Uma fundição usou pela primeira vez núcleos de areia revestidos com sílica para produzir coletores de escapamento de aço resistentes ao calor.Devido à alta temperatura de vazamento (1470-1550°C), os núcleos de areia foram facilmente deformados, resultando em fenômenos fora da tolerância na espessura da parede do tubo.Embora a areia de sílica tenha sido tratada com mudança de fase em alta temperatura, devido à influência de vários fatores, ela ainda não consegue superar a deformação do núcleo de areia em alta temperatura, resultando em uma ampla gama de flutuações na espessura da parede do tubo , e em casos graves, será descartado.A fim de melhorar a resistência do núcleo de areia e controlar a geração de gás do núcleo de areia, decidiu-se usar areia revestida com areia cerâmica.Quando a quantidade de resina adicionada foi 36% menor do que a areia revestida com sílica, sua resistência à flexão à temperatura ambiente e resistência à flexão térmica aumentou em 51%, 67%, e a quantidade de geração de gás é reduzida em 20%, o que atende aos requisitos requisitos de processo de alta resistência e baixa geração de gás.
A fábrica usa núcleos de areia revestidos com sílica e núcleos de areia revestidos com cerâmica para fundição simultânea, após a limpeza das peças fundidas, eles realizam inspeções anatômicas.
Se o núcleo for feito de areia revestida com sílica, as peças fundidas têm espessura de parede irregular e parede fina, e a espessura da parede é de 3,0-6,2 mm;quando o núcleo é feito de areia revestida com areia de cerâmica, a espessura da parede da fundição é uniforme e a espessura da parede é de 4,4-4,6 mm.como segue a imagem
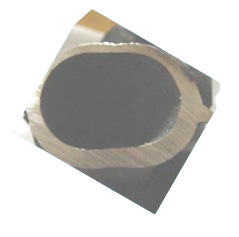
Areia revestida com areia de sílica
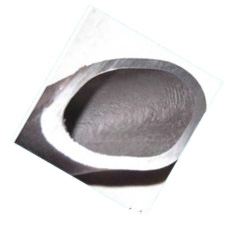
Areia revestida com areia de cerâmica
Areia revestida com areia de cerâmica é usada para fazer núcleos, o que elimina a quebra do núcleo de areia, reduz a deformação do núcleo de areia, melhora muito a precisão dimensional do canal de fluxo da cavidade interna do coletor de escape e reduz a aderência de areia na cavidade interna, melhorando a qualidade de fundidos e taxa de produtos acabados e alcançado benefícios econômicos significativos.
3. Aplicação de areia cerâmica na carcaça do turbocompressor
A temperatura de trabalho na extremidade da turbina do invólucro do turbocompressor geralmente excede 600°C, e alguns atingem até 950-1050°C.O material da casca precisa ser resistente a altas temperaturas e ter bom desempenho de fundição.A estrutura da casca é mais compacta, a espessura da parede é fina e uniforme, e a cavidade interna é limpa, etc., é extremamente exigente.Atualmente, a carcaça do turbocompressor é geralmente feita de aço fundido resistente ao calor (como 1.4837 e 1.4849 da norma alemã DIN EN 10295) e também é usado ferro dúctil resistente ao calor (como o padrão alemão GGG SiMo, o americano ferro nodular austenítico padrão de alto teor de níquel D5S, etc.).
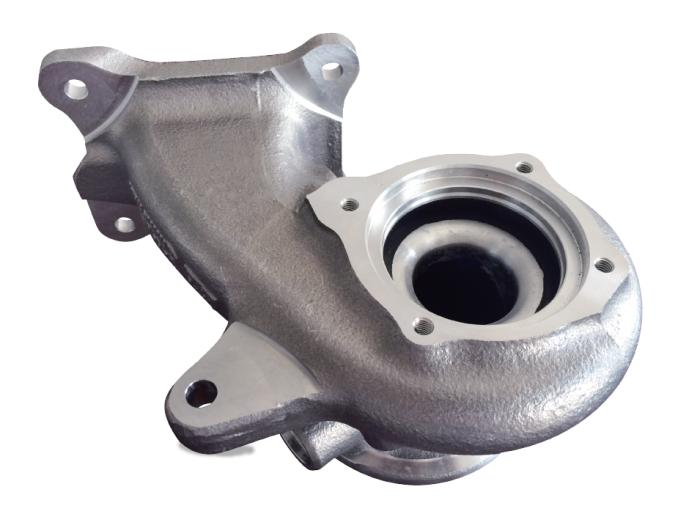
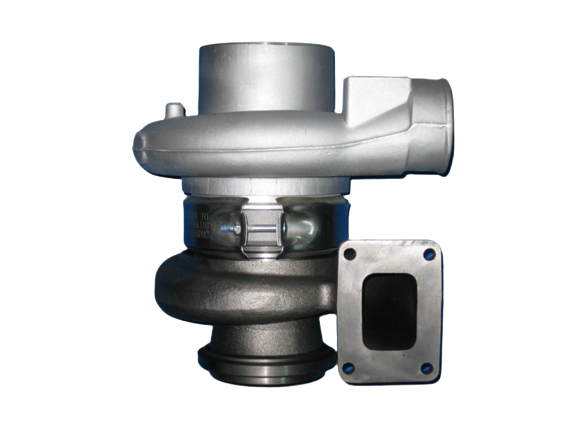
Uma carcaça do turbocompressor do motor de 1,8 T, material: 1,4837, ou seja, GX40CrNiSi 25-12, composição química principal (%): C: 0,3-0,5, Si: 1-2,5, Cr: 24-27, Mo: Max 0,5, Ni: 11 -14, temperatura de vazamento 1560 ℃.A liga tem um alto ponto de fusão, uma grande taxa de encolhimento, uma forte tendência a rachaduras a quente e alta dificuldade de fundição.A estrutura metalográfica da peça fundida possui exigências rígidas quanto a carbonetos residuais e inclusões não metálicas, havendo também normas específicas sobre defeitos de fundição.A fim de garantir a qualidade e a eficiência da produção de peças fundidas, o processo de moldagem adota a fundição de núcleo com núcleos de casca de areia revestidos com filme (e alguns núcleos de caixa fria e caixa quente).Inicialmente, foi usada areia de lavagem AFS50 e, em seguida, areia de sílica torrada, mas problemas como aderência de areia, rebarbas, rachaduras térmicas e poros na cavidade interna apareceram em graus variados.
Com base em pesquisas e testes, a fábrica decidiu usar areia de cerâmica.Inicialmente comprou areia revestida acabada (100% areia de cerâmica) e, em seguida, adquiriu equipamento de regeneração e revestimento e otimizou continuamente o processo durante o processo de produção, use areia de cerâmica e areia de depuração para misturar areia bruta.Atualmente, a areia revestida é implementada aproximadamente de acordo com a tabela a seguir:
Processo de areia revestida com cerâmica para carcaça do turbocompressor | ||||
Tamanho da areia | Taxa de % de areia cerâmica | % de adição de resina | Resistência à flexão MPa | Saída de gás ml/g |
AFS50 | 30-50 | 1.6-1.9 | 6,5-8 | ≤12 |
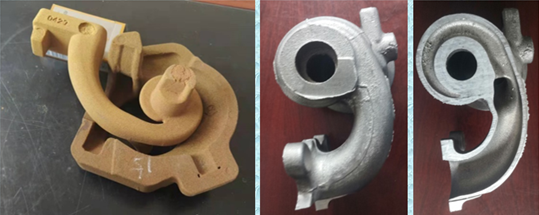
Nos últimos anos, o processo de produção desta fábrica tem funcionado de forma estável, a qualidade dos fundidos é boa e os benefícios econômicos e ambientais são notáveis.O resumo é o seguinte:
a.Usando areia de cerâmica, ou usando uma mistura de areia de cerâmica e areia de sílica para fazer núcleos, elimina defeitos como aderência de areia, sinterização, veios e rachaduras térmicas de fundidos, e realiza uma produção estável e eficiente;
b.Fundição do núcleo, alta eficiência de produção, baixa relação areia-ferro (geralmente não mais que 2:1), menor consumo de areia bruta e custos mais baixos;
c.O vazamento do núcleo é propício para a reciclagem geral e regeneração de resíduos de areia, e a recuperação térmica é adotada uniformemente para regeneração.O desempenho da areia regenerada atingiu o nível de areia nova para areia de lavagem, que conseguiu o efeito de reduzir o custo de compra de areia bruta e reduzir a descarga de resíduos sólidos;
d.É necessário verificar frequentemente o teor de areia cerâmica na areia regenerada para determinar a quantidade de nova areia cerâmica adicionada;
e.A areia de cerâmica tem forma arredondada, boa fluidez e grande especificidade.Quando misturado com areia de sílica, é fácil causar segregação.Se necessário, o processo de disparo de areia precisa ser ajustado;
f.Ao cobrir o filme, tente usar resina fenólica de alta qualidade e use vários aditivos com cuidado.
4. Aplicação de areia cerâmica no cabeçote de liga de alumínio do motor
A fim de melhorar a potência dos automóveis, reduzir o consumo de combustível, reduzir a poluição do escapamento e proteger o meio ambiente, os automóveis leves são a tendência de desenvolvimento da indústria automobilística.Atualmente, as peças fundidas de motores automotivos (incluindo motores a diesel), como blocos de cilindros e cabeçotes, são geralmente fundidas com ligas de alumínio, e o processo de fundição de blocos e cabeçotes de cilindros, quando se usa núcleos de areia, fundição por gravidade em molde de metal e baixa pressão fundição (LPDC) são os mais representativos.
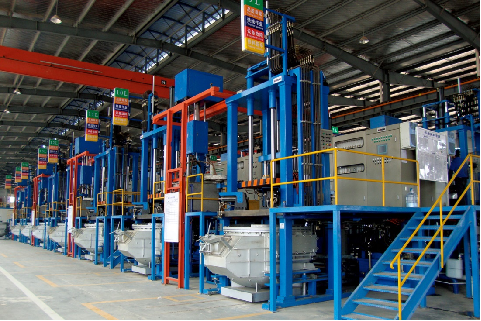
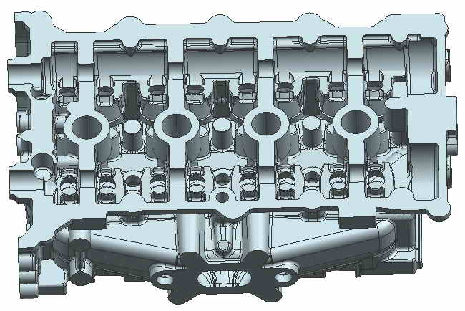
O processo de núcleo de areia, areia revestida e caixa fria do bloco de cilindros de liga de alumínio e peças fundidas de cabeça são mais comuns, adequados para características de produção de alta precisão e em larga escala.O método de utilização da areia cerâmica é semelhante ao da produção de cabeçotes de ferro fundido.Devido à baixa temperatura de vazamento e à pequena gravidade específica da liga de alumínio, geralmente é usada areia de núcleo de baixa resistência, como um núcleo de areia de caixa fria em uma fábrica, a quantidade de resina adicionada é de 0,5-0,6% e a resistência à tração é 0,8-1,2 MPa.Areia de núcleo é necessária Tem boa colapsibilidade.O uso de areia cerâmica reduz a quantidade de resina adicionada e melhora muito o colapso do núcleo de areia.
Nos últimos anos, a fim de melhorar o ambiente de produção e melhorar a qualidade das peças fundidas, há cada vez mais pesquisas e aplicações de aglutinantes inorgânicos (incluindo vidro de água modificado, aglutinantes de fosfato, etc.).A imagem abaixo é o local de fundição de uma fábrica usando cabeça de cilindro de liga de alumínio de núcleo de areia inorgânica de cerâmica.
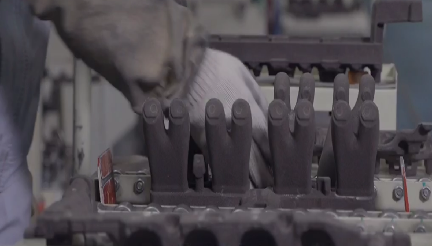
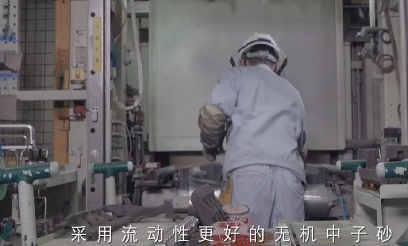
A fábrica usa aglutinante inorgânico de areia de cerâmica para fazer o núcleo, e a quantidade de aglutinante adicionada é de 1,8 a 2,2%.Devido à boa fluidez da areia de cerâmica, o núcleo de areia é denso, a superfície é completa e lisa e, ao mesmo tempo, a quantidade de geração de gás é pequena, melhora muito o rendimento das peças fundidas, melhora a colapsibilidade da areia do núcleo , melhora o ambiente de produção e se torna um modelo de produção verde.
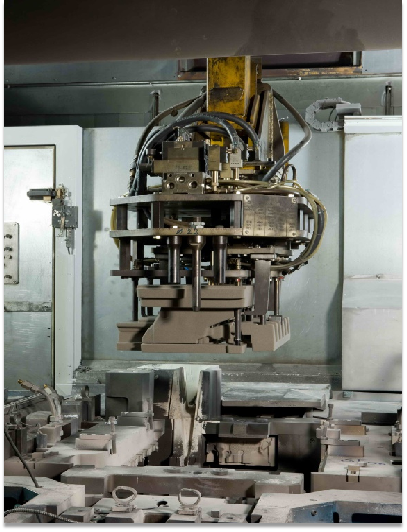
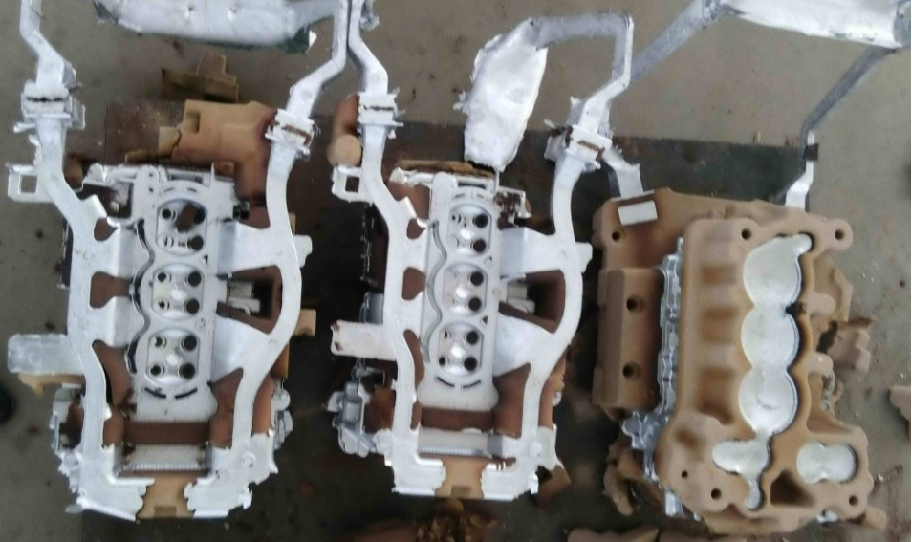
A aplicação de areia cerâmica na indústria de fundição de motores melhorou a eficiência da produção, melhorou o ambiente de trabalho, resolveu defeitos de fundição e alcançou benefícios econômicos significativos e bons benefícios ambientais.
A indústria de fundição de motores deve continuar a aumentar a regeneração da areia do núcleo, melhorar ainda mais a eficiência do uso da areia cerâmica e reduzir as emissões de resíduos sólidos.
Do ponto de vista do efeito de uso e escopo de uso, a areia de cerâmica é atualmente a areia especial de fundição com o melhor desempenho abrangente e o maior consumo na indústria de fundição de motores.
Horário da postagem: 27 de março de 2023